Value Stream Mapping: A Powerful Tool for Business Transformation
Organisations are constantly seeking ways to streamline their processes and deliver greater value to their customers. One powerful tool that has gained traction across various industries is Value Stream Mapping (VSM). Originally developed as part of the lean manufacturing tool kit, VSM has proven to be an invaluable method for visualising and optimising workflows, identifying inefficiencies and highlighting the largest areas of opportunity within an end-to-end process. This blog delves into the concept of Value Stream Mapping, explores its benefits and challenges, and offers practical insights for effectively implementing VSM in business services processes. Whether you're new to VSM or looking to refine your approach, this comprehensive guide will provide the knowledge and tools needed to harness the full potential of this transformative methodology.
What is Value Stream Mapping?
Value Stream Mapping (VSM) is a visual tool used to analyse and design the flow of materials and information required to bring a product or service to the customer. Originating from the lean manufacturing tool kit, VSM helps identify waste, streamline processes, and improve overall efficiency. It involves mapping out every step in a process, both value-adding and non-value-adding, to gain a comprehensive view of the workflow. The ultimate goal is to optimise the value delivered to the customer while minimising resources and time.
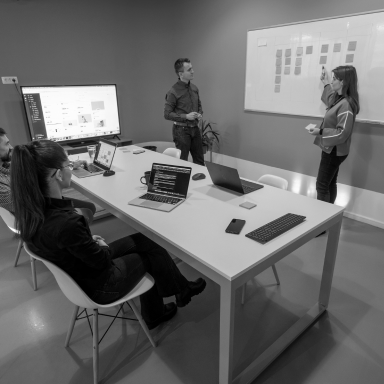
Benefits of Value Stream Mapping in Business Services Processes
- Enhanced Visibility and Transparency: VSM provides a holistic view of processes, making it easier to identify bottlenecks, duplications and inefficiencies. This visibility enables better decision-making and prioritisation of improvement efforts.
- Improved Process Efficiency: By highlighting non-value-adding activities, VSM helps organisations streamline workflows, reduce waste, and shorten cycle times. This leads to cost savings and faster delivery of services.
- Customer-Centric Focus: VSM encourages a focus on the customer's needs and expectations. By aligning processes with customer value, businesses can enhance service quality and customer satisfaction.
- Collaboration and Communication: The mapping process fosters collaboration among team members and departments. It creates a common understanding of processes, enabling better communication and alignment of goals.
- Continuous Improvement: VSM is a foundation for continuous improvement initiatives. It provides a baseline for measuring progress and assessing the impact of changes over time.
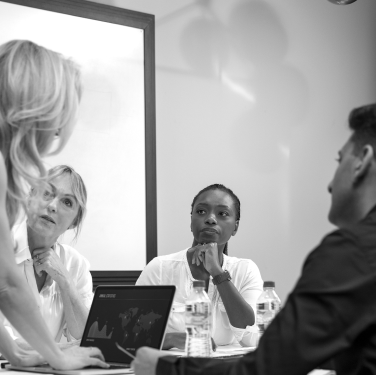
Common Pitfalls of Value Stream Mapping in a Non-Manufacturing Context
- Overlooking Service-Specific Nuances: Unlike manufacturing, service processes often involve intangible outputs and high variability. Failing to account for these differences can lead to oversimplification and inadequate mapping. Adapt VSM tools and techniques to fit the unique characteristics of service processes. This may involve focusing on information flow, customer interactions, and service delivery pathways rather than physical flows.
- Lack of Detailed Data: In service industries, data may not be as readily available or quantifiable as in manufacturing. This can make it challenging to accurately map processes and identify areas for improvement. Collect data which makes sense for your particular process, don’t worry about technical lean calculations unless they will help to visualise areas for improvement.
- Resistance to Change: Employees in non-manufacturing sectors may be less familiar with lean methodologies. This unfamiliarity can lead to resistance, scepticism, or lack of engagement. To overcome a lack of understanding, organisations could invest some time in training individuals on Lean principals. Workshops, case studies, and hands-on exercises can help demystify VSM and build competency. Involve key stakeholders from the outset to build buy-in and reduce resistance. Clear communication about the purpose and benefits of VSM can help address concerns and align expectations.
- Underestimating the Complexity of Service Processes: Services often involve complex, cross-functional processes with multiple touchpoints. Neglecting these complexities can result in incomplete or inaccurate value stream maps. Make sure you collaborate across multiple departments or teams, it’s very rare for an end-to-end process to be confined to one operational team. Or may also want to start with small, manageable projects to demonstrate the value of VSM. Success in these pilot projects can build momentum and confidence for broader implementation.
Value Stream Mapping in Remote or Hybrid Work Environments
The rise of remote and hybrid work models presents both challenges and opportunities for VSM. While the lack of physical presence can complicate mapping efforts, digital tools and virtual collaboration platforms can effectively bridge the gap.
- Virtual Collaboration Tools: Leverage online tools such as virtual whiteboards, project management software, and video conferencing to facilitate collaborative mapping and action planning sessions. These tools can replicate the experience of in-person workshops and allow for real-time input and discussion.
- Asynchronous Collaboration: In a hybrid or remote setting, it may not always be possible to gather all stakeholders at the same time. Asynchronous methods, such as sharing documents and collecting feedback over time, can be effective in ensuring broad participation.
- Clear Documentation and Communication: With dispersed teams, it's crucial to maintain clear and comprehensive documentation of the VSM process. This includes detailed maps, process descriptions, and action plans. Clear communication helps keep everyone on the same page and ensures that improvements are implemented consistently.
- Adaptation to Digital Workflows: Recognise the shift towards digital workflows and incorporate these into the VSM process. This includes mapping out digital tools, software applications, and information flows that are now integral to remote work.
Conclusion
Value Stream Mapping is a powerful methodology that can significantly enhance process efficiency and customer satisfaction across various industries, including non-manufacturing sectors. While challenges such as lack of familiarity and the complexity of service processes exist, these can be effectively managed through education, stakeholder engagement, and the use of digital tools. In an increasingly remote and hybrid work environment, adapting VSM practices to fit new ways of working ensures that organisations continue to optimise their processes and deliver maximum value to their customers.
I recently recorded a webinar on this topic. Watch the recording here.